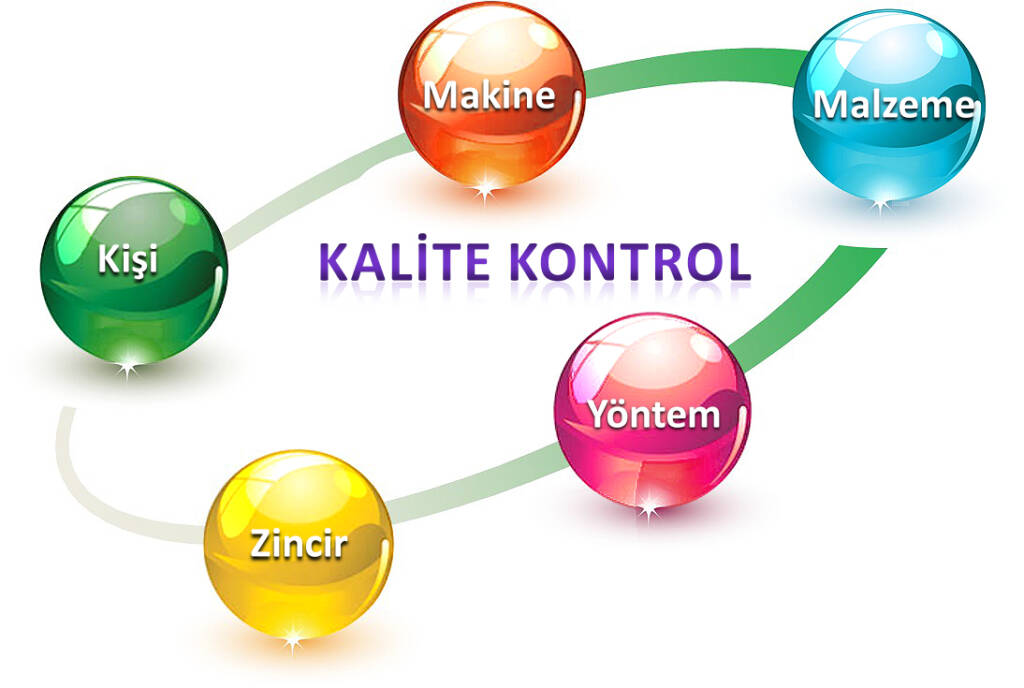
Our Quality Management Policy.
In addition to the quality control policies and tests that we apply as standard in our production, special production methods and different tests can be applied upon the request of our customers. Some of the non-destructive tests we have applied are as follows:
- Radiographic Examination (RT): Radioactive radiation, which is emitted from a controllable radiation source with a certain characteristic and amount, weakens as it passes through the test piece. If there is a discontinuity in the area it passes through, the discontinuity will cause the photographic film to darken in a different color.
- Ultrasonic Examination (UT): Ultrasonic inspection is used to identify defects within the material (even if they are deep) in cases where X-ray inspection is not possible or meaningful, especially in parts with large wall thicknesses (< 20 mm) and in joining shapes (HV / DHV – Welded T joint).
- Liquid Penetrant Testing (PT): Liquid Penetrant testing is a frequently used method for determining discontinuities that are open to the surface. The principle of Liquid Penetrant testing is that the Penetrant liquid, which has a strong contrast effect, makes very small defects visible on the developer layer.
- Magnetic Particle Inspection (MPI): The magnetic particle method is used to detect surface and near-surface discontinuities and only in ferromagnetic parts. The basic principle is based on the magnetization of the test material by passing alternating and direct electric current or direct magnetic current. If there is any discontinuity in the tested part of the part, the magnetic flux lines deviate from the discontinuity due to the permeability difference and an intense leakage field is formed on the fault.